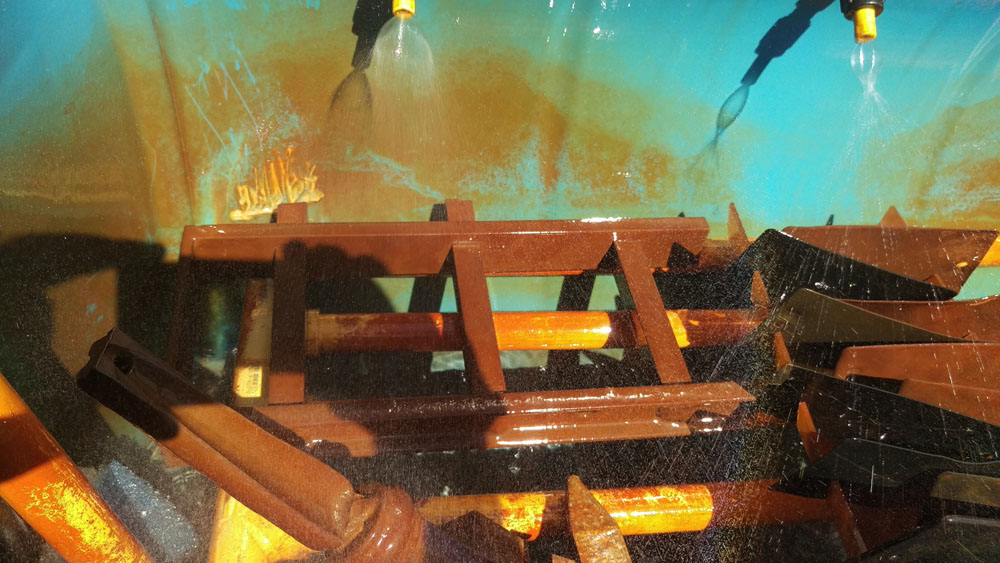
For years, here at Compass Ironworks, we had relied on outside testing labs to provide us feedback on the durability of our powder coat finishes, especially as it pertains to the harsh elements at the shore. In 2013, Compass created our own in-house salt spray testing within the guidelines of ASTM B-117, but with added UV exposure and variable temperature. Temperature varied from below freezing to as high as 138 degrees Fahrenheit. Ocean Water Salinity is typically 3.2 to 3.8%. Our salinity was kept at 5%, which subjected the test pieces to harsher conditions than real life.
The industry test standards are based on ASTMB-117, AAMA 2603 (1,500 hours of resistance) AAMA 2604 (3,000 hours of resistance) and AAMA 2605 (4,000 hours of resistance). Some of our test pieces took all this abuse in stride and looked as pristine as they started after an amazing 20,000 hours! All the pieces were scribed (the finish was cut to allow the harsh salt composition an access point under the finish). The real test is when the salt has ready access under the finish, to see if the finish is tight enough to the substrate below that there is no creepage.
There were a whole host of materials tested: Cor-ten, ductile Iron casting, gray Iron casting, Marine Grade Aluminum casting, Aircraft Grade Aluminum, and Hot Dip Galvanizing. Various pretreatment processes were also tested, as well as blast vs. no blast, and physical etch vs. chemical etch.
“This salt spray test lab has given us incredible insight in surface preparation, pretreatment chemical composition and powder coating application. It really gives us the assurance that we can provide cutting edge quality for our client’s project,” says Amos Glick, President of Compass Ironworks. Compass Ironworks customers can be assured their projects will withstand the elements for a much greater time length than is typical!
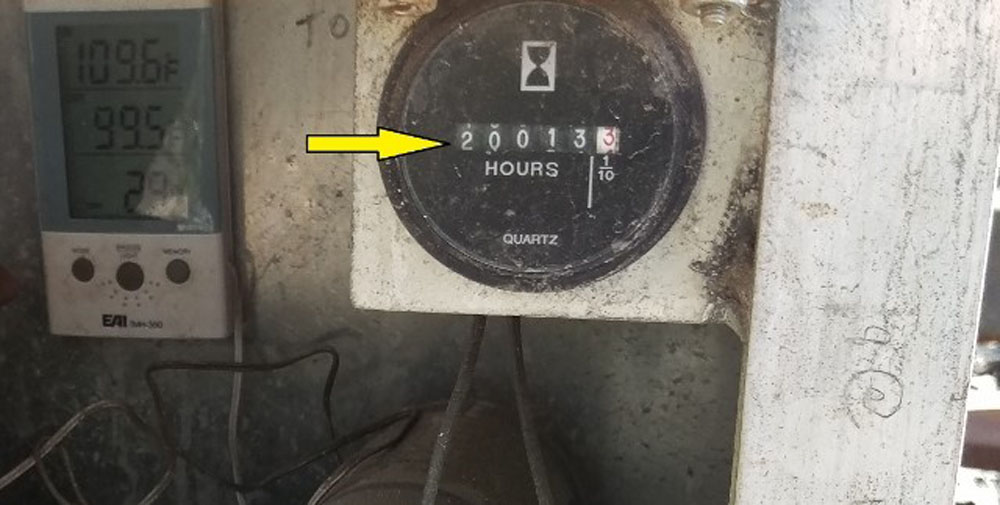
AAMA 2603 is typically an interior specification, such as ceiling panels and supports and interior windows. 2603 powders offer good resistance to abrasion, scratching and scuffing, but should be applied where color retention is not required.
AAMA 2604 is an “intermediate” specification. This finish will provide good color and gloss retention for approximately five years of exposure.
AAMA 2605 is the high-performance exterior specification. These finishes are resistant to moisture, weathering, ozone and UV radiation. An application for this finish would include architectural projects that require long term cosmetic and functional protection.