Longevity
Withstanding the Elements
- For interior applications – iron or A-36 steel can be used without any corrosion concerns. The use of other metals, such as bronze, stainless, or aluminum, is for visual enhancement.
- For exterior applications – iron or A-36 steel can be used, but in most of the U.S., corrosion is a serious concern. In the southwest, however, corrosion is not an issue due to less rainfall.
Ensuring longevity, while being eco-sensitive:
To ensure longevity, the metal must be completely sealed from the elements. Our powder coat is eco-friendly, as it’s VOC-free and 99.99% reclaimable. Its electrostatic application can wrap around the part, making it easy to apply to designs that are relatively simple and straightforward.
For projects with very intricate scrollwork, this electrostatic method creates a “Faraday Cage” effect — it will not easily penetrate inside tight areas. By heating the railing at 200°F and manually spraying powder into tight areas, that effect can be overcome. There is, however, still a chance that over the years, there may be some leaching of corrosion from these inside areas, potentially staining your beautiful terrace or property.
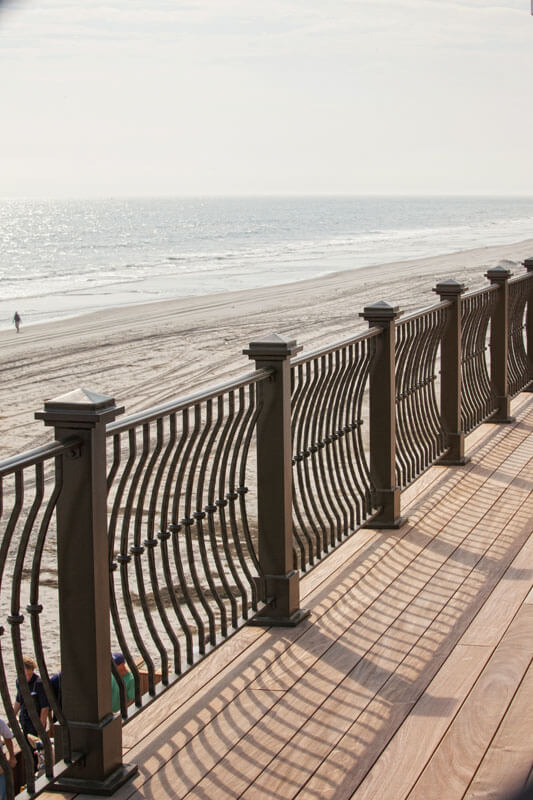
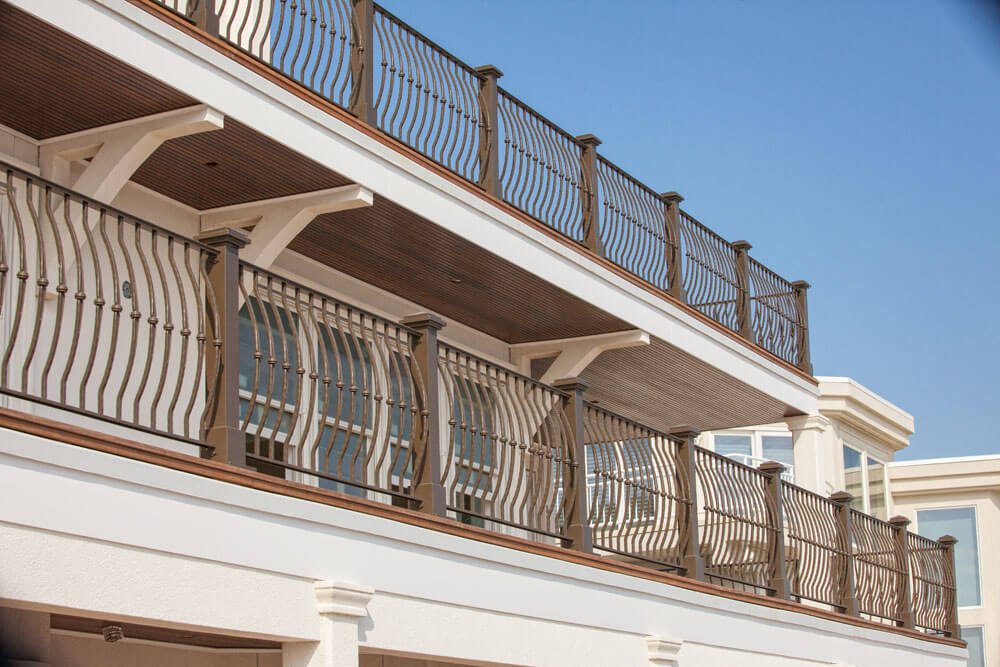
Durability
COMPLETE COVERAGE
For complete coverage, the project needs to be completely dipped in zinc at 835°F. This will create four microscopic layers; the outside layer being pure zinc. This completely encapsulates the metal, flows into the inside areas, and provides peace of mind regarding corrosion. The challenge with raw galvanizing is threefold:
- Drips and rough areas on the surface – this is addressed with visual inspection and manual sanding of those areas.
- Raw galvanizing – doesn’t offer enough of a profile to which the powder-coat can adhere. This is offset by brush blasting before powder.
- Trapped gases inherent in the substrate after undergoing drastic temperature changes from galvanizing. This is addressed by preheating the part to a temperature higher than the cure temperatures of the powder-coat.
This duplex process of powder-coat over hot-dip galvanizing provides the feel and authenticity of wrought iron. The resultant finish gets its texture and character from industrial imperfections inherent in galvanizing and the matte black powder-coat. It truly resembles a project created a century ago.
We can also use solid aircraft grade aluminum for exteriors; when powder-coated correctly, it is indistinguishable from iron. Most people are averse to the look of poor quality aluminum, but typically gloss is associated with aluminum for the simple reason that production aluminum companies often used gloss powder for mass-produced items. As a result, gloss is often associated with lower grade aluminum product. By using a matte or flat black powder, it completely obliterates the feel of aluminum and assumes the regality of iron. The four most popular colors are: semi-gloss black, matte black or flat black and statuary bronze.
Metals
Materials
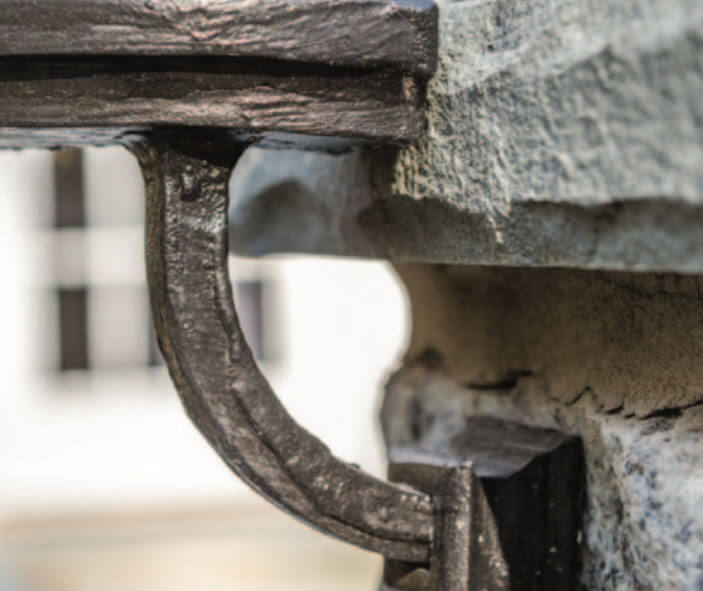
CIW 1775-I
Antique paint finish for iron or steel or wrought material.
For today’s iron or A-36 steel, a finish that looks centuries old, painted and repainted to match the craftsmanship and detail of the 1775 era. This has the visual aspect of being painted and repainted numerous times.
Steps:
- Blast to SSPC-SP 5/NACE No. 1, white metal blast.
- Pretreat for galvanize as per ASTM A123.
- Galvanize as per ASTM A385.
- Visual inspection of surfaces; drips, runs and blemishes sanded for conformity of
depth within +/- 1/32”. - Brush blast to SSPC-SP 7/NACE No. 4, brush-off last leaning.
- Heated phosphate wash, MetaplexTM Phosplex 16, titrated to pH 4.
- Clean water rinse; dissolved solids must be less than 150 ppm.
- Chemical sealer, E-CLPS® 1980, applied per manufacturer’s specifications.
- Preheat to 200°F.
- Special paint and reheat process has globbed appearance and actual brush marks.
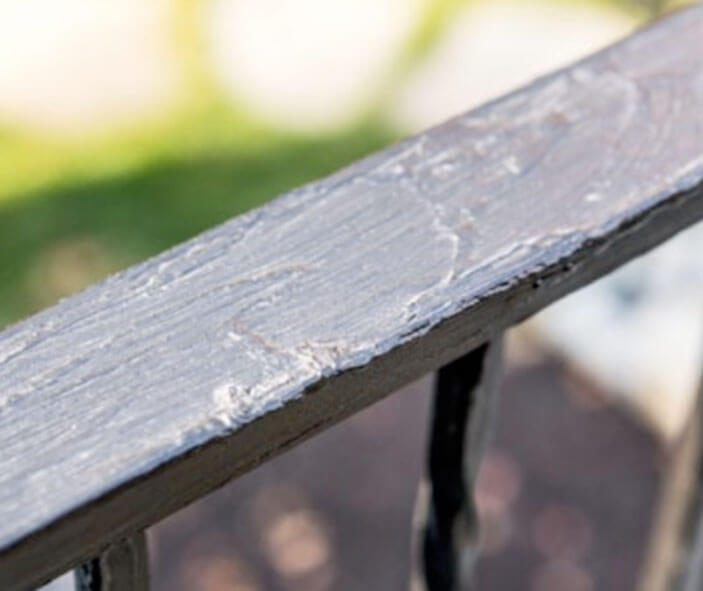
CIW 1775-A
Antique paint finish specification for ASTM 6061 or 6063 Aluminum. This has the visual aspect of being painted and repainted numerous times.
Steps:
- Blast to SSPC-SP 5/NACE No. 1, white metal blast.
- Heated phosphate wash, Metaplex Phosplex 16, titrated to pH 4.
- Clean water rinse; dissolved solids must be less than 150 ppm.
- Chemical sealer, E-CLPS 1980, applied per manufacturer’s specifications.
- Preheat to 200°F.
- Special paint and reheat process has globbed appearance and actual brush marks.
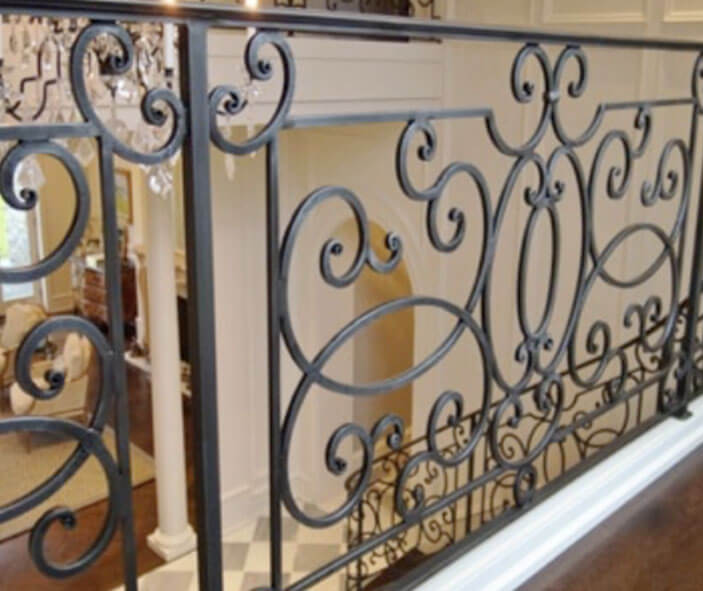
CIW 1895
Traditional blackened wax finish. For interior only; can be applied on wrought iron or A-36 steel or wrought material.
Steps:
- Blast to SSPC-SP 5/NACE No. 1, white metal blast.
- Immerse in JAX® Chemicals M-24 for 60 seconds
- Brush with stiff plastic bristled brush for consistency if needed.
- Immerse in neutralizing solution, comprised of 1 tsp. of sodium bicarbonate per quart of water.
- Air or towel dry only. Do not heat.
- Rub entire piece with Penetrol® penetrating oil using towels.
- Sand with 3M coarse Scotch-BriteTM pads for silver contrast. Use sample piece for comparison.
- Heat to 110°F.
- While maintaining heat, use rags to apply natural yellow, unbleached beeswax over entire surface.
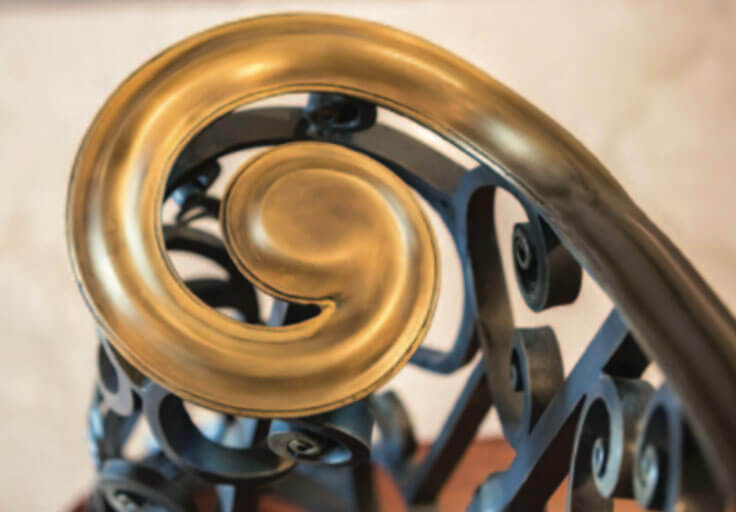
CIW 1995-B
385000 Architectural Bronze is the correct material to be specified; for the antique tarnished look of brass rail created 100 years ago.
Steps:
- Sand with 3M Scotch-Brite with coarse wheel to remove any deep blemishes.
- Sand with 3M Scotch-Brite fine wheel for visual smoothness.
- Sand with 3M Scotch-Brite pad to create consistent line or grain direction.
- Heat to 100° F and apply JAX Chemicals.
- Brush with stiff plastic bristle brush for consistency.
- Immerse in neutralizing solution, comprised of 1 tsp. of sodium bicarbonate per quart of water.
- Sand with Scotch-Brite pads until correct shade; it’s important to only go on direction as all marks will show.
- Wipe clean with thinner rag.
- Heat until 130°F.
- Apply Renaissance Wax.
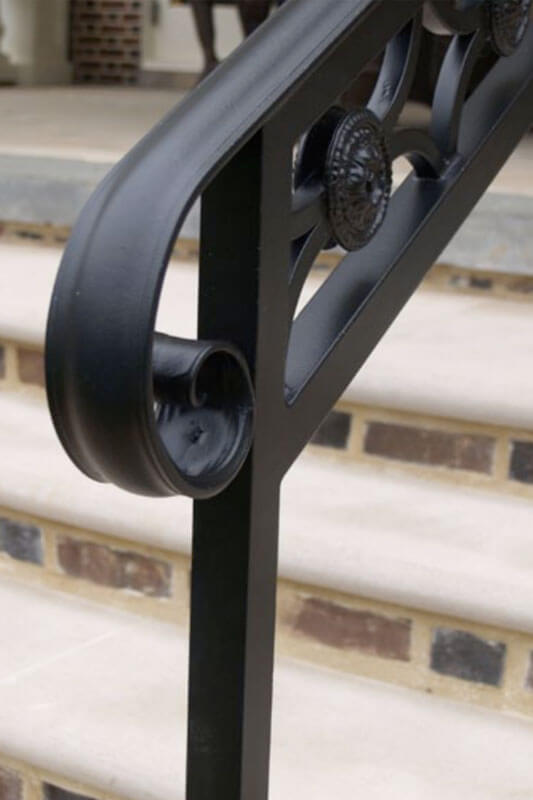
CIW 2135-I
Steel or Iron Galvanized Duplex System or Wrought Material.
For today’s iron or A-36 steel that looks century’s old. There will be some imperfections on the surface due to the inherent inconsistency of hot-dip galvanizing. This will give it a very high level of authenticity. Corrosion will be a non-issue, however, inter-coat adhesion is an issue; step #5 offsets that. DOT rates this Duplex System at 120 years to 20% failure.
Steps:
- Blast to SSPC SSPC-SP 5/NACE No. 1, white metal blast.
- Pretreat as per ASTM A123.
- Galvanize as per ASTM A385.
- Visual inspection of surfaces; drips, runs and blemishes sanded for conformity of depth
- within +/- 1/32”.
- Brush blast to SSPC-SP 7/NACE No. 4, brush-off blast cleaning.
- Heated phosphate wash, Metaplex Phosplex 16, titrated to pH 4.
- Chemical Sealer, E-CLPS 1980, applied per manufacturer’s specifications.
- Preheat to 200oF.
- 1 coat of Top-Coat Powder-Coat, Super Durable Series 38 from TIGER Drylac®, applied per manufacturer’s specifications.
- 2nd coat of Top-Coat Powder-Coat, Super Durable Series 38 from TIGER Drylac, applied per manufacturer’s specifications.
- Cure at 390°F for 15 minutes within +/- 5°.
- Visual inspection to ensure no blemishes.
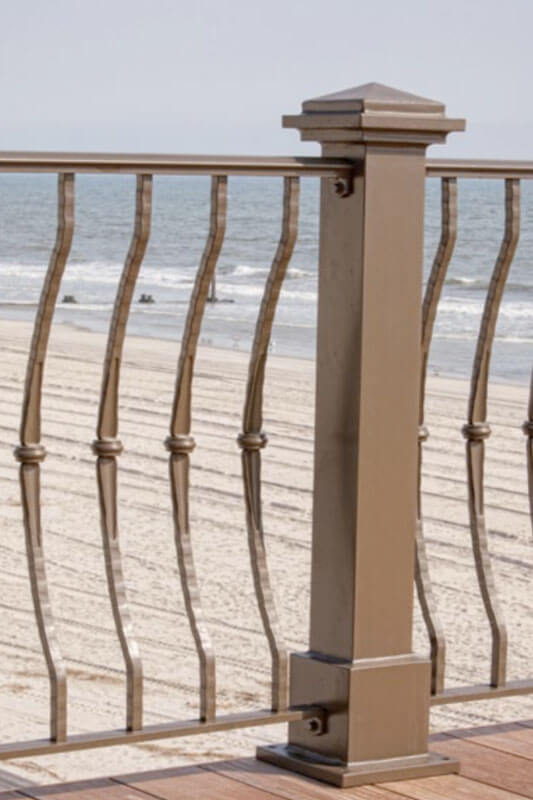
CIW 2604-A
Powder-coated metal finish for Stainless Steel 316 or Aluminum.
Steps:
- Blast to SSPC SSPC-SP 5/NACE No. 1
- Heated phosphate wash, Metaplex Phosplex 16, titrated to pH 4.
- Clean water rinse; dissolved solids must be less than 150 ppm.
- Chemical Sealer, E-CLPS 1980, applied per manufacturer’s specifications.
- Epoxy Zinc-free Primer, DryProtector from Tiger-Drylac 69/70000.
- Preheat to 200°F +-/10°.
- 1 coat of Top-Coat Powder-Coat, Super Durable Series 38 from TIGER Drylac (or equivalent), applied per manufacturer’s specifications.
- 2nd coat of Top-Coat Powder-coat, Super Durable Series 38 from TIGER Drylac (or equivalent), applied per manufacturer’s specifications.
- Cure at 390°F for 15 minutes within +/- 5°.
- Visual inspection to ensure no blemishes.
For ASTM 6061 or 6063 Aluminum or 316 Stainless Steel in harsh waterfront conditions. AAMA 2604 rates this at 1,000 hours, measured under ASTM b117 salt fog testing.
*NOT AVAILABLE IN IRON*
For iron in harsh waterfront conditions, the proper specification is CIW 2135-I. The CIW 2604 finish can be used for decades of maintenance-free beauty on iron, A-36 Steel, or aluminum projects installed away from bodies of water. Depending on the level of scroll intricacy, any iron or steel project may need CIW 2135-I, as powder-coat is applied electrostatically and may not be able to penetrate tight corners or cavities due to the “Faraday Cage” effect.
Double Helical & Spiral Staircases
Designer Staircase Attributes
Just as elegant as they are durable, our double helical stairs and spiral staircases far exceed the quality and beauty of stair kits. These luxury designer staircases can be fully customized to your vision with high-quality materials and unique designs.
Standing out against the competition, our double helical and spiral staircases share the following attributes:
- Custom Designs
- Lightweight
- Fully Welded Unit
- Custom Laser-Cut & Formed Treads
- Outside Skirt
- Space-Efficient
- Anti-Corrosive Materials
View our double helical stairs and spiral staircase brochures for more information.
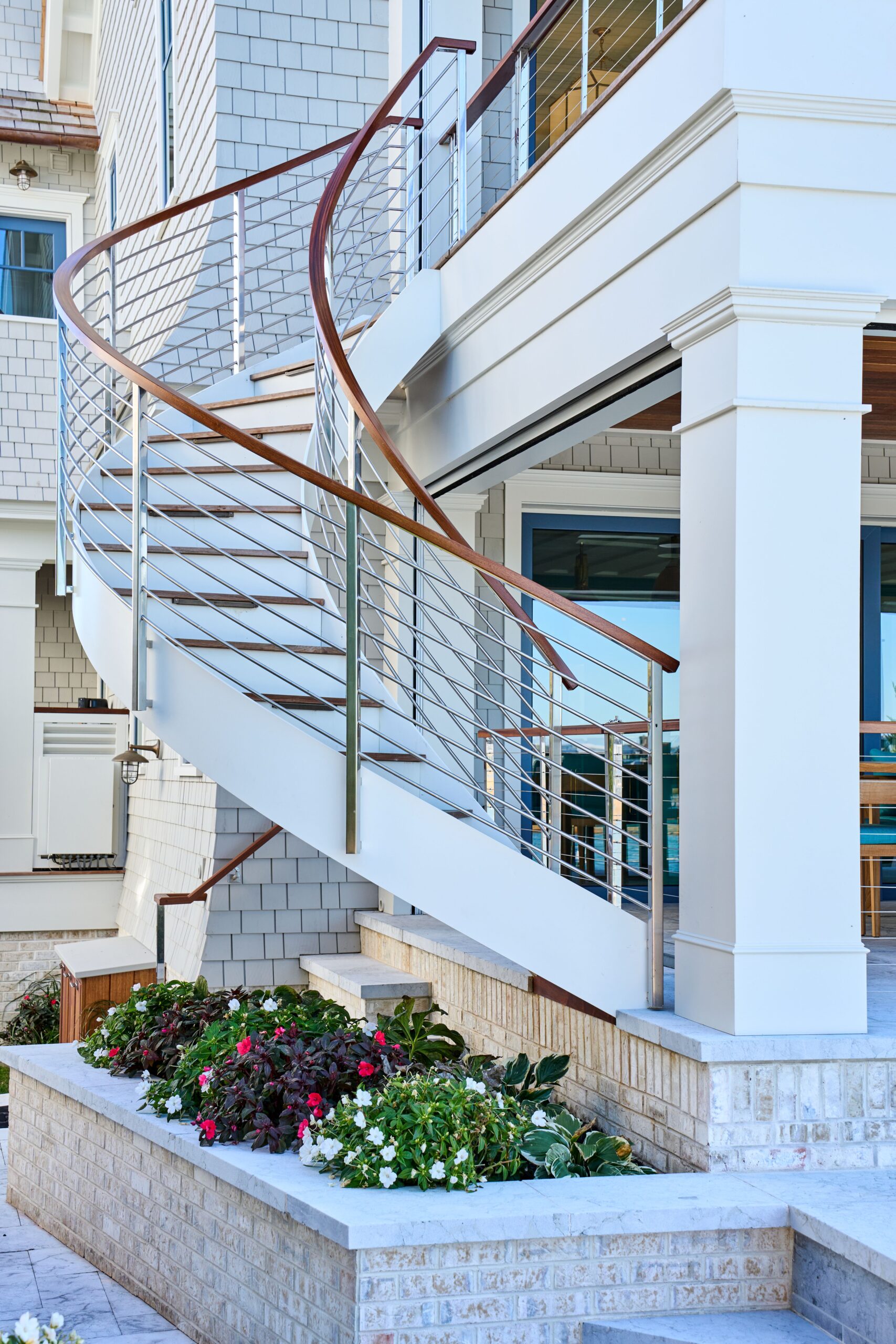
Design
Complimentary
Design Guide
Our Design Guide provides a wide portfolio of Compass Ironworks creations. Simply identify designs that you like and give us a call for a no-obligation consultation.
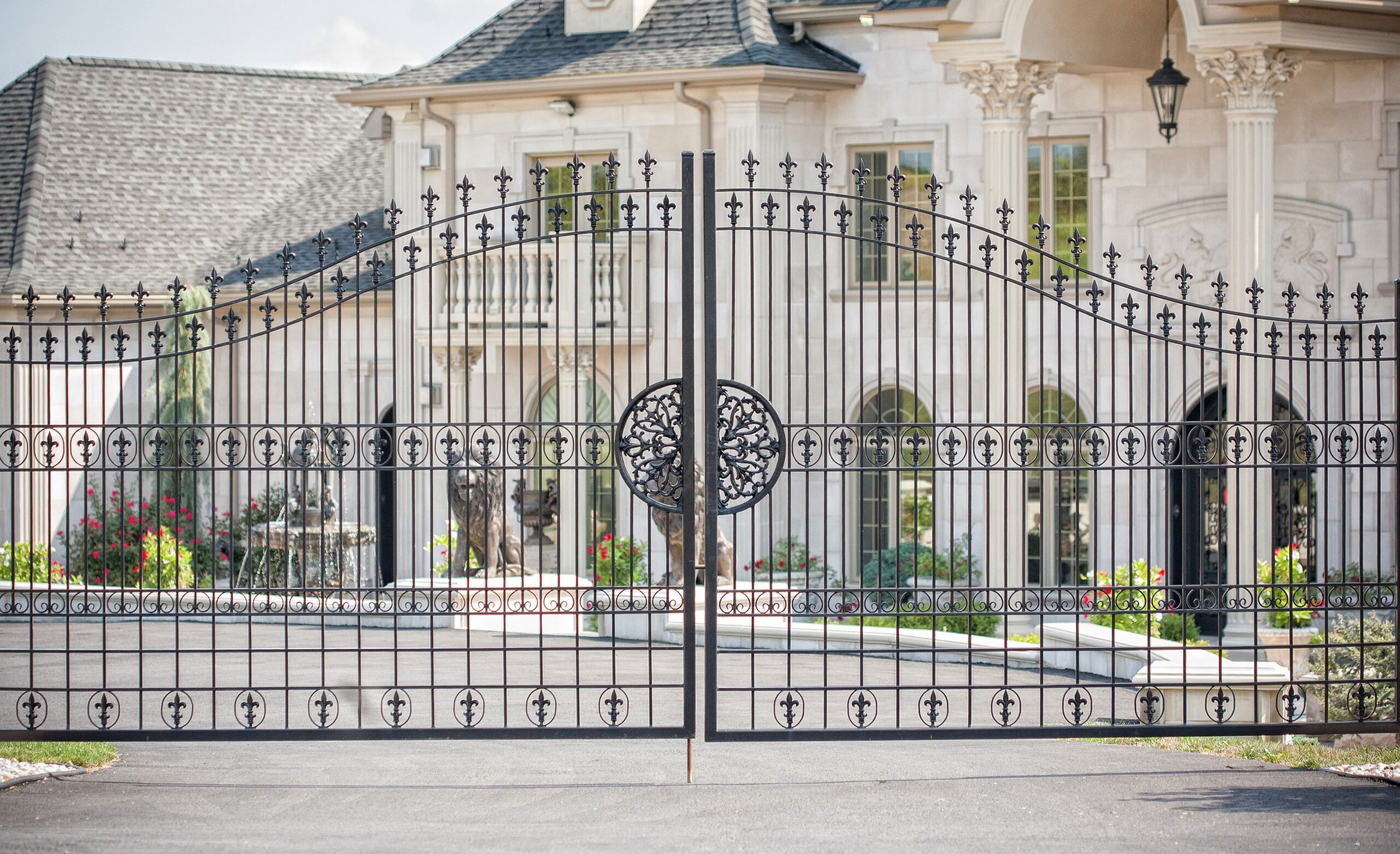